Mama Bhanja represents a revolutionary end-to-end ERP solution developed by AaiNova for a leading Diesel Exhaust Fluid (DEF) manufacturer with operations spanning across India. The comprehensive system integrates seven critical business functions—raw material management, manufacturing, distribution, sales, transportation, marketing, and accounting—into a unified digital ecosystem that eliminated data silos and manual processes that had previously hampered growth.
By implementing this tailored solution, AaiNova transformed the client’s fragmented operations into a streamlined, data-driven enterprise with real-time visibility across the entire value chain. The multi-module approach ensures seamless information flow between company-owned stores, franchise locations, transporters, drivers, and administrative staff, creating unprecedented operational efficiency while providing management with actionable insights through comprehensive reporting and analytics.
Increase in overall production efficiency after full implementation
reduction in operational costs across manufacturing and distribution
decrease in inventory discrepancies between physical counts and system records
faster order fulfillment time from manufacturing to customer delivery
The Chalange
The DEF manufacturer operated with disconnected systems across their production facilities, warehouses, and retail outlets, causing significant data inconsistencies and reporting delays. This fragmentation created blind spots in inventory tracking, making it impossible to optimize raw material orders and production schedules effectively.
Their expanding network of company-owned and franchise stores lacked standardized processes for sales reporting and inventory management. Manual reconciliation created bottlenecks that slowed business growth and made it difficult to implement loyalty initiatives or track marketing effectiveness across different regions.
Transportation logistics remained a major pain point, with manual dispatch systems and paper-based documentation causing delivery delays and customer dissatisfaction. The inability to track vehicles in real-time or optimize routes resulted in elevated fuel costs and inefficient asset utilization throughout their distribution network.
What did AaiNova do
AaiNova developed an integrated ERP solution with five specialized applications targeting distinct operational areas: admin, sales, driver, transporter, and marketing functions. Each module was designed to address specific business requirements while maintaining seamless data integration across the entire ecosystem.
The team implemented comprehensive production tracking that follows raw materials from receipt through manufacturing to finished goods inventory. The system captures real-time data at every touchpoint, enabling accurate forecasting, quality control monitoring, and production optimization across all manufacturing facilities.
AaiNova created a robust point-based loyalty system integrated directly with the sales application, incentivizing both direct customers and franchise operators. The marketing module provides campaign management tools with performance analytics, while transportation modules optimize routing and provide real-time visibility of product movements throughout the supply chain
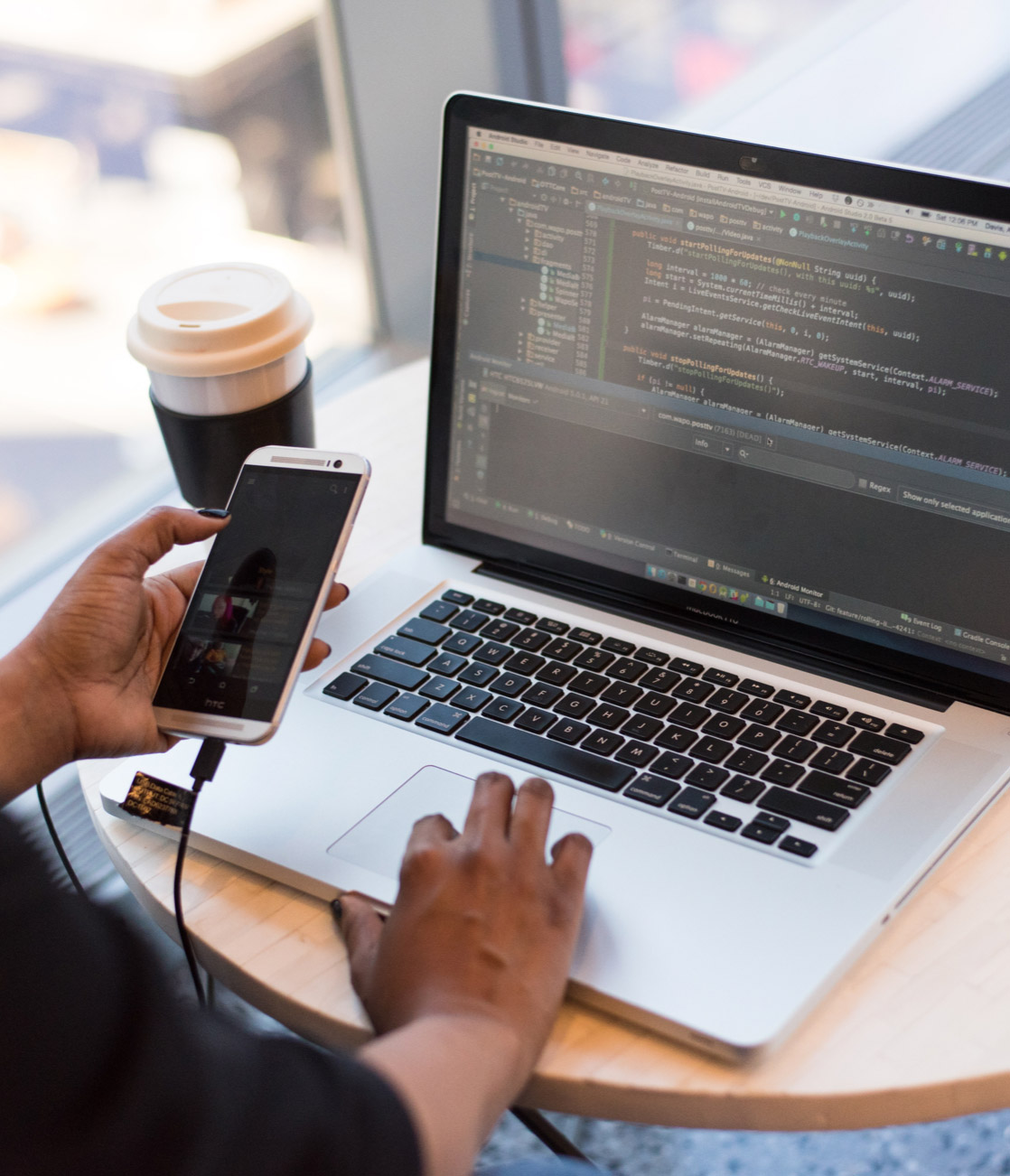
The Results
- Created an end-to-end ERP solution integrating 7 critical business functions into a unified digital ecosystem
- Reduced operational costs by 32% through process automation and elimination of manual data entry
- Increased production efficiency by 47% through improved raw material management and production scheduling
- Decreased inventory discrepancies by 78%, virtually eliminating stock-outs and overstock situations
- Improved cash flow by reducing the order-to-cash cycle from 12 days to just 3.5 days
- Enabled data-driven decision making with comprehensive real-time reporting across all business units